Design & Technology Discussion
This blog article mainly discuss our efforts put on designing all of our forged wheels. Explaining some un-noticeable differences in terms of designs and technologies compare to other street use products.
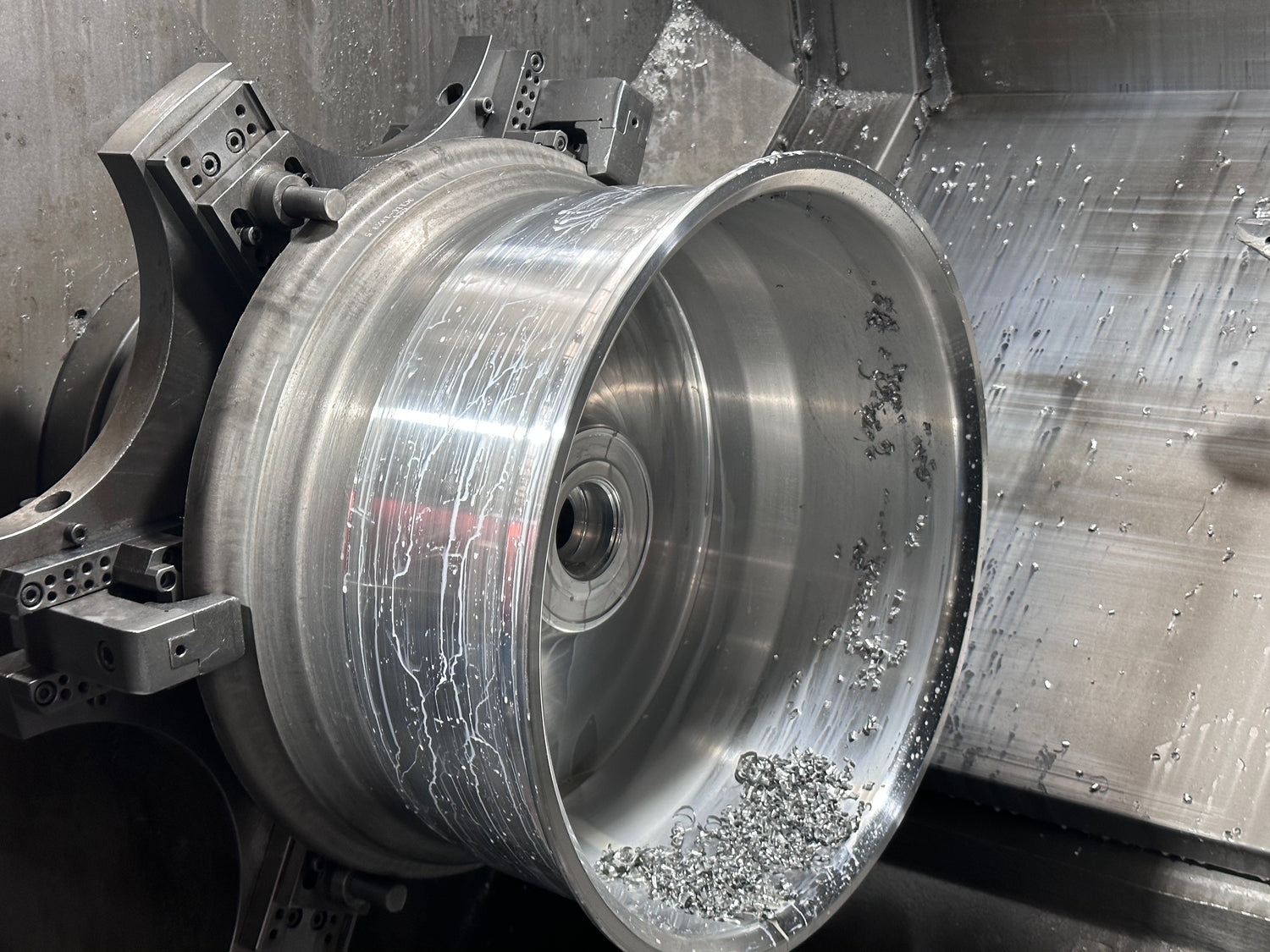
No Compromise
Forge to Win
Fabricated through a meticulous process of 10,000-ton pressure forging using 6061-T6 aluminum, guaranteeing unmatched strength and durability. Redesigned the barrel shape to protect the tire while aggressive driving to the best extent. More materials were used in the barrel.
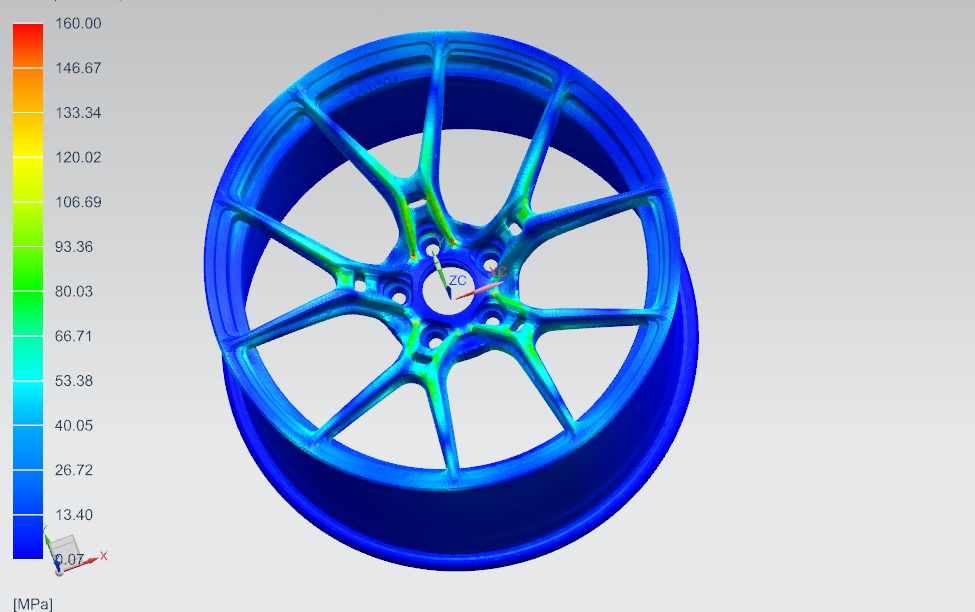
Optimization
Structual Design
Our wheels have undergone rigorous Finite Element Analysis (FEA), and in house strength&tensile testing, validating their capacity to withstand pressures exceeding 1550 pounds. Concurrently, these wheels exhibit an impressive strength-to-weight ratio, rendering them remarkably lightweight without compromising on durability.
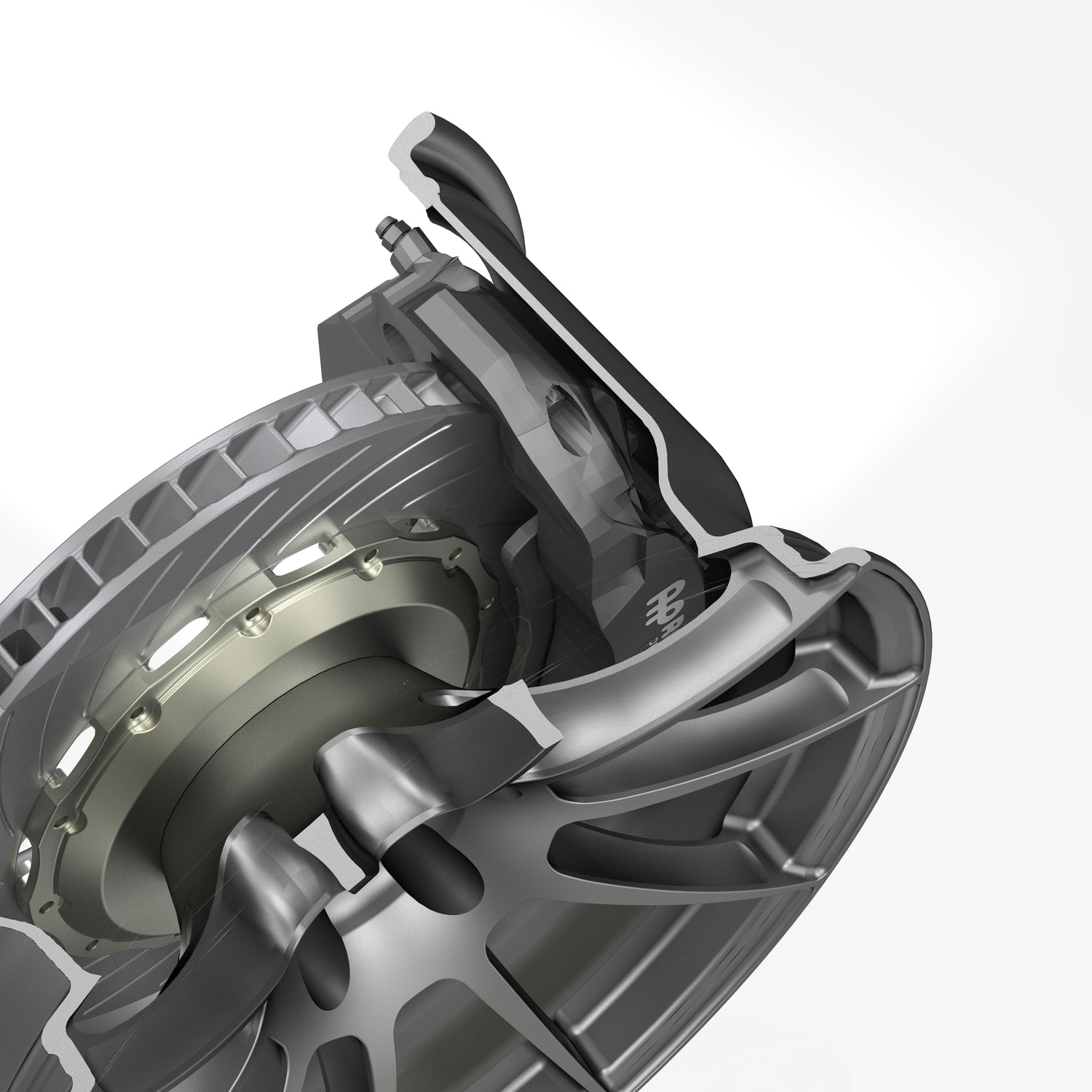
Racing standard
Brake Clearance
Our redesigned barrel shape allows us to optimize brake clearance, acknowledging the performance benefits of smaller wheels and larger brakes for faster lap times. Adhering to ETRTO standards, our innovative design ensures enough space even with substantial components like an 18x11 ET10 rim, AP Racing Pro-5000R CP9665 Caliper, and 380mm brake rotor. Say goodbye to brake interference worries and welcome an enhanced racing experience.
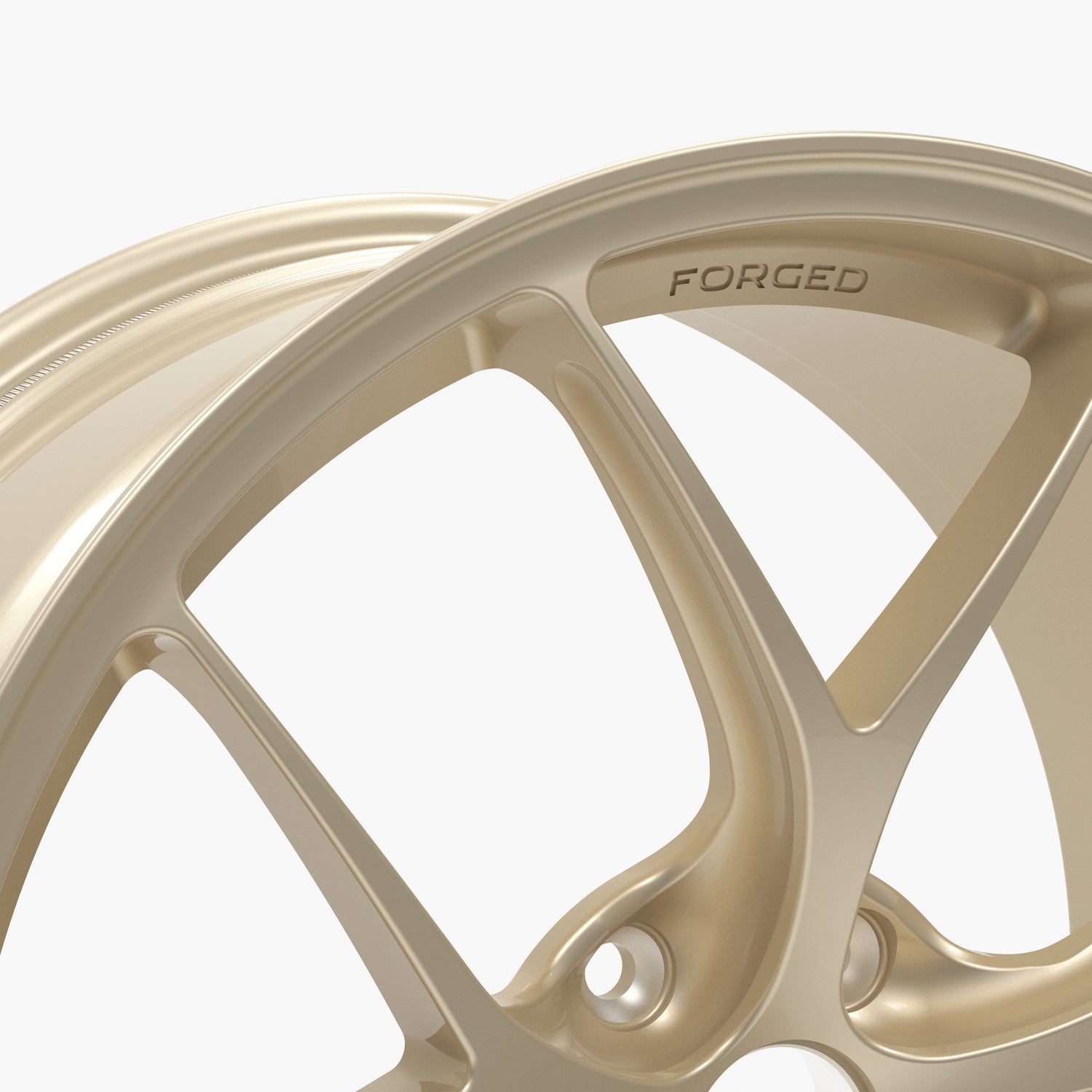
Best Weight to Strength Ratio
Side-Milled Spoke
The implementation of precision-engineered thin side-milled spokes serves to optimize both the aesthetics and performance of the wheel, culminating in a harmonious balance of style and function.
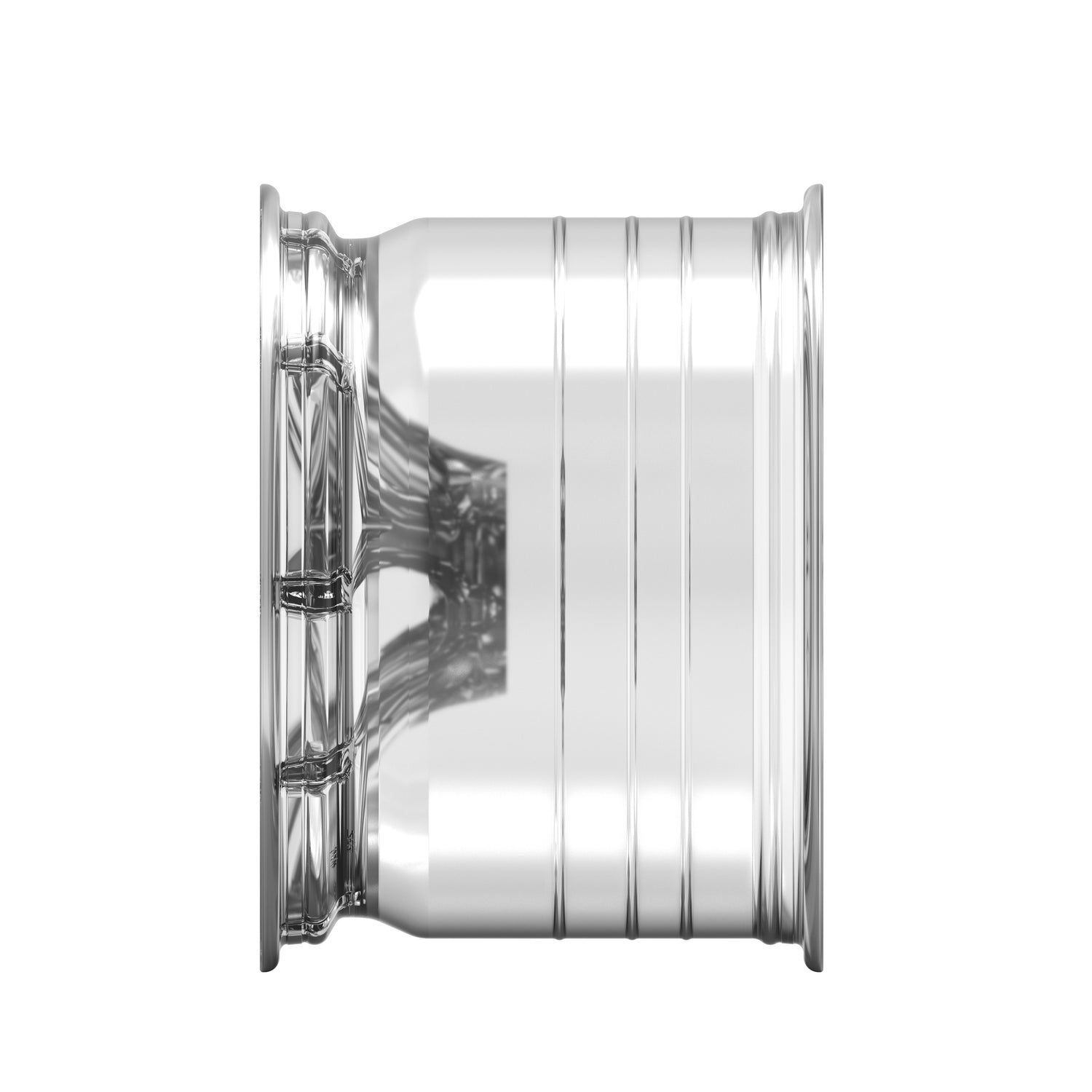
Deep Concativity
The functionality of deep wheel concavity pertains to the operational effectiveness and structural dynamics inherent in the profound curvature of a wheel's surface.
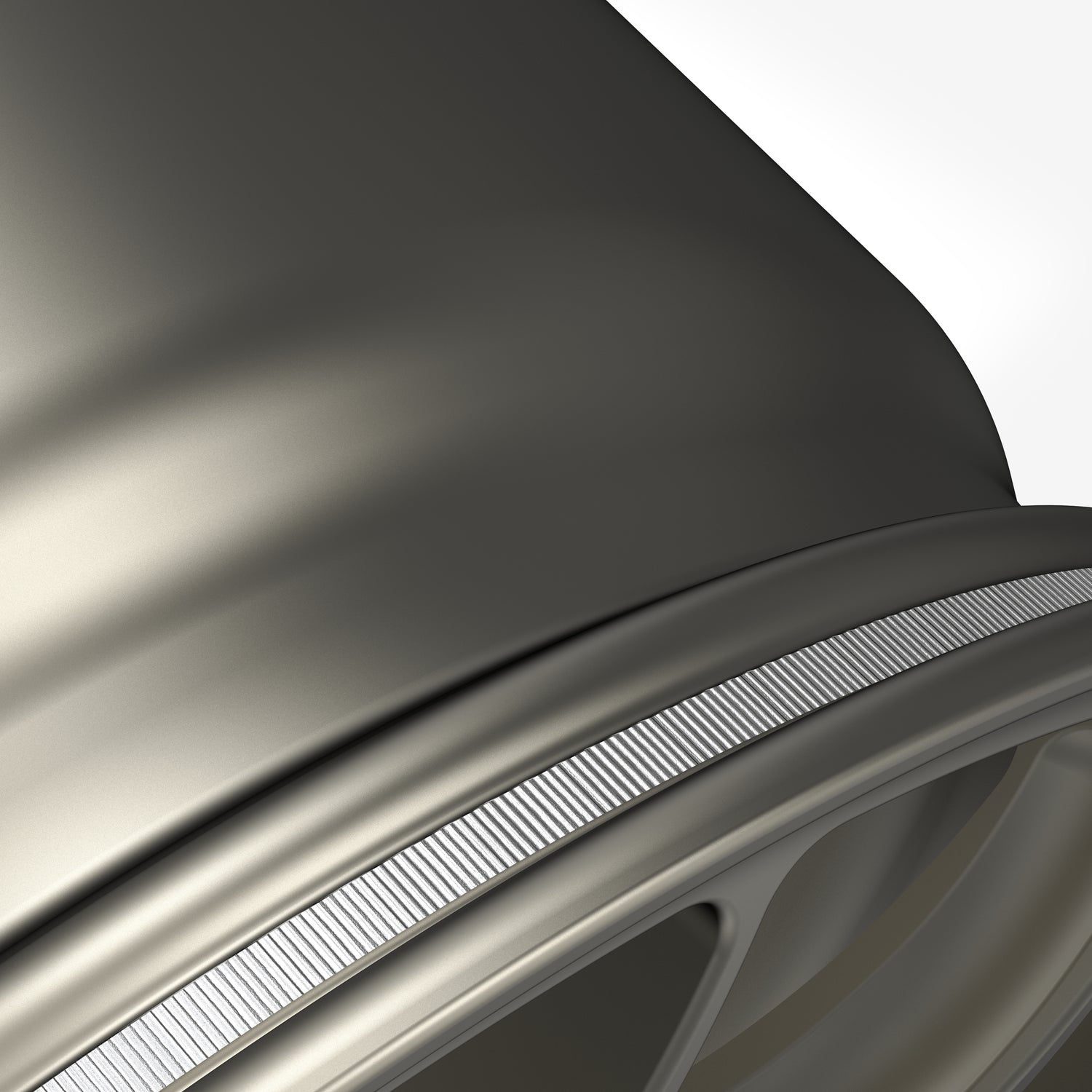
Maximum grip
Paintless Knurled Beads
During aggressive driving, tire and wheel slippage can compromise grip. Our solution: unpainted knurled beads on forged aluminum wheels. Unlike competitors, we leave these beads bare except for a thin protective layer. This preserves their sharpness, enhancing friction and preventing slippage, maximizing grip during high-speed maneuvers.
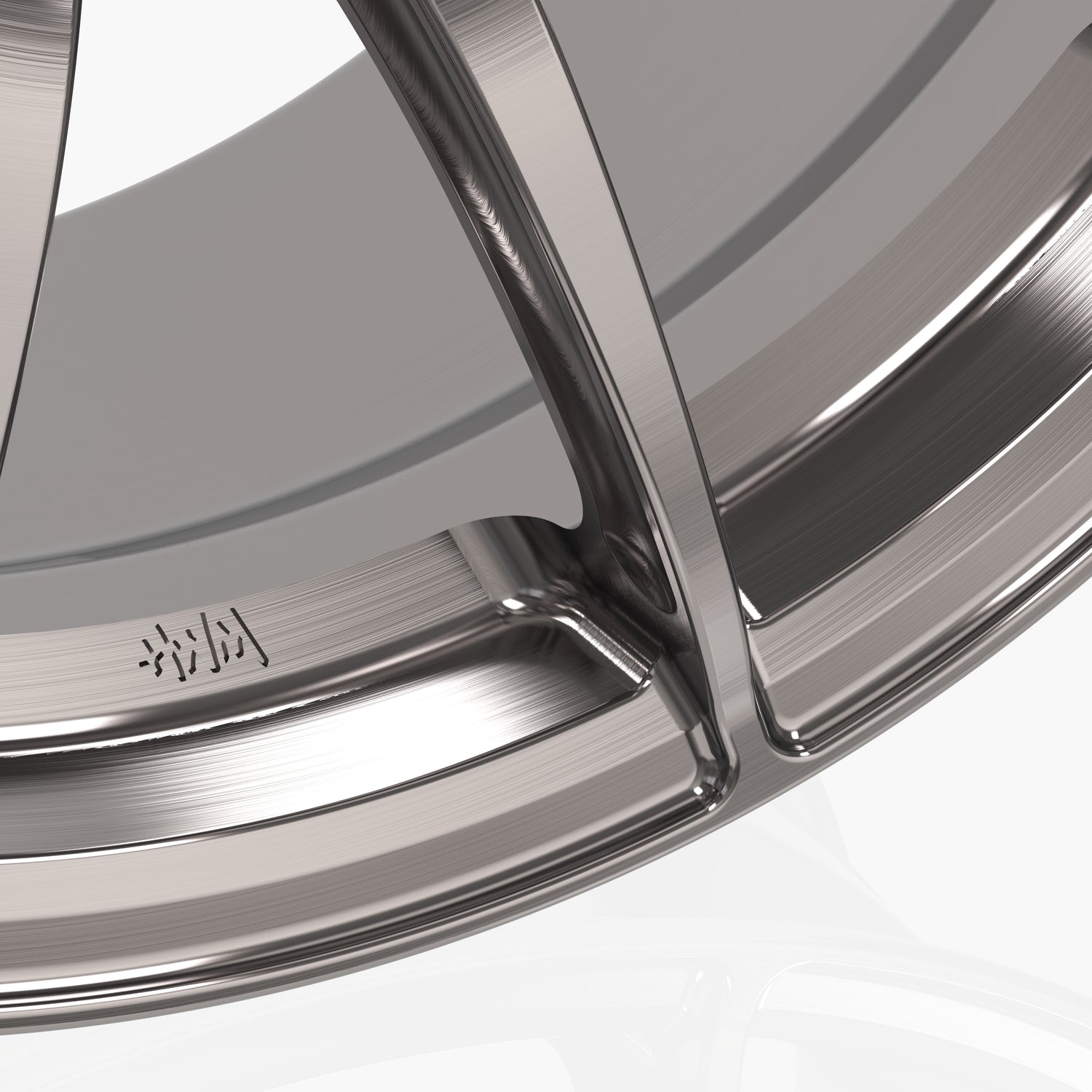
Reinforced Spoke
We've implemented additional reinforcement in the wheel spoke. Our approach involves carefully balancing the properties of strength, stiffness, weight, and cost. Our primary focus has always been maintaining this delicate equilibrium. Despite a slight increase in both cost and weight, this modification results in a wheel with heightened resistance to flex and fatigue.
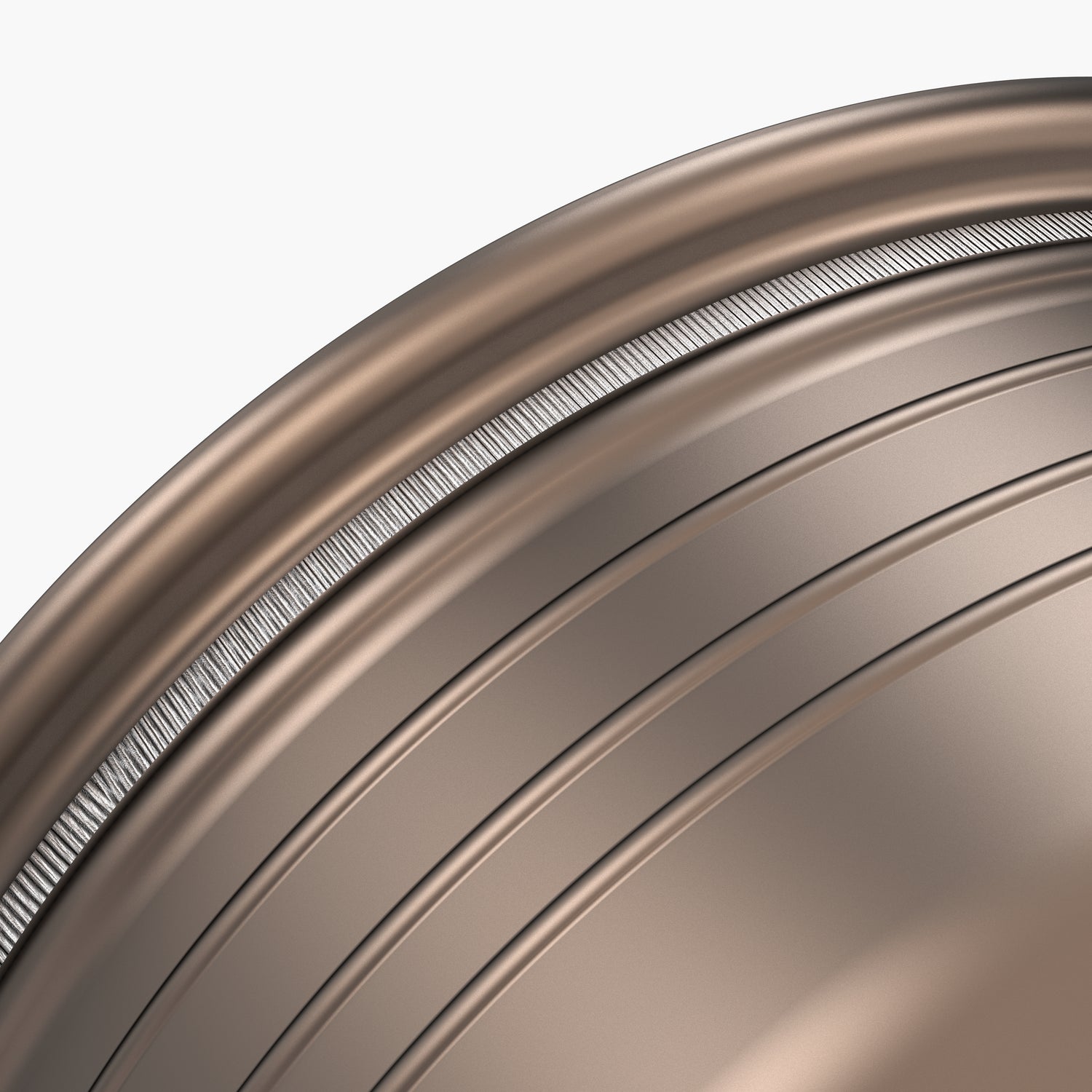
Reinforced Barrel
The inclusion of reinforcement ribs in the design of a wheel barrel serves to fortify its structural framework, imparting increased strength and resilience to withstand heavy loads and prolonged use. These ribs, strategically positioned along the body of the barrel, distribute weight more evenly and prevent deformation or failure under stress. Their presence underscores a commitment to durability and efficiency, essential qualities for effective material transport and handling operations.
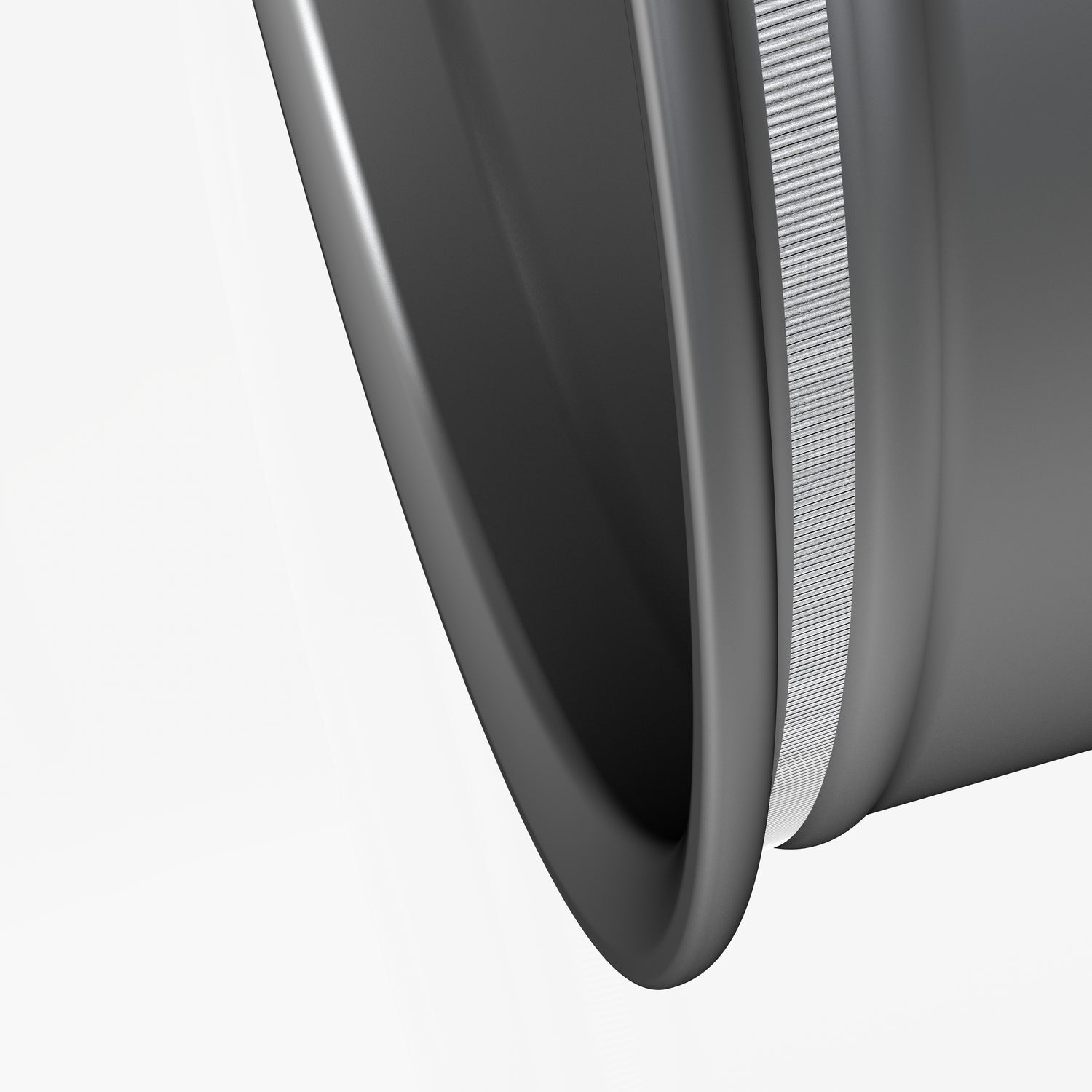
Thicker Inner Lip
The thick inner lip design incorporates a robust rim construction featuring a notably wide inner edge. This design element bolsters the rim's durability and resilience against impacts and loads, enhancing overall wheel performance and longevity. By prioritizing a substantial inner lip, we optimize the rim's ability to withstand stresses and maintain structural integrity under demanding conditions, such as off-road driving or heavy-duty applications. This design choice ensures greater reliability and safety, providing peace of mind for users who rely on their wheels to withstand rugged terrain or challenging environments.
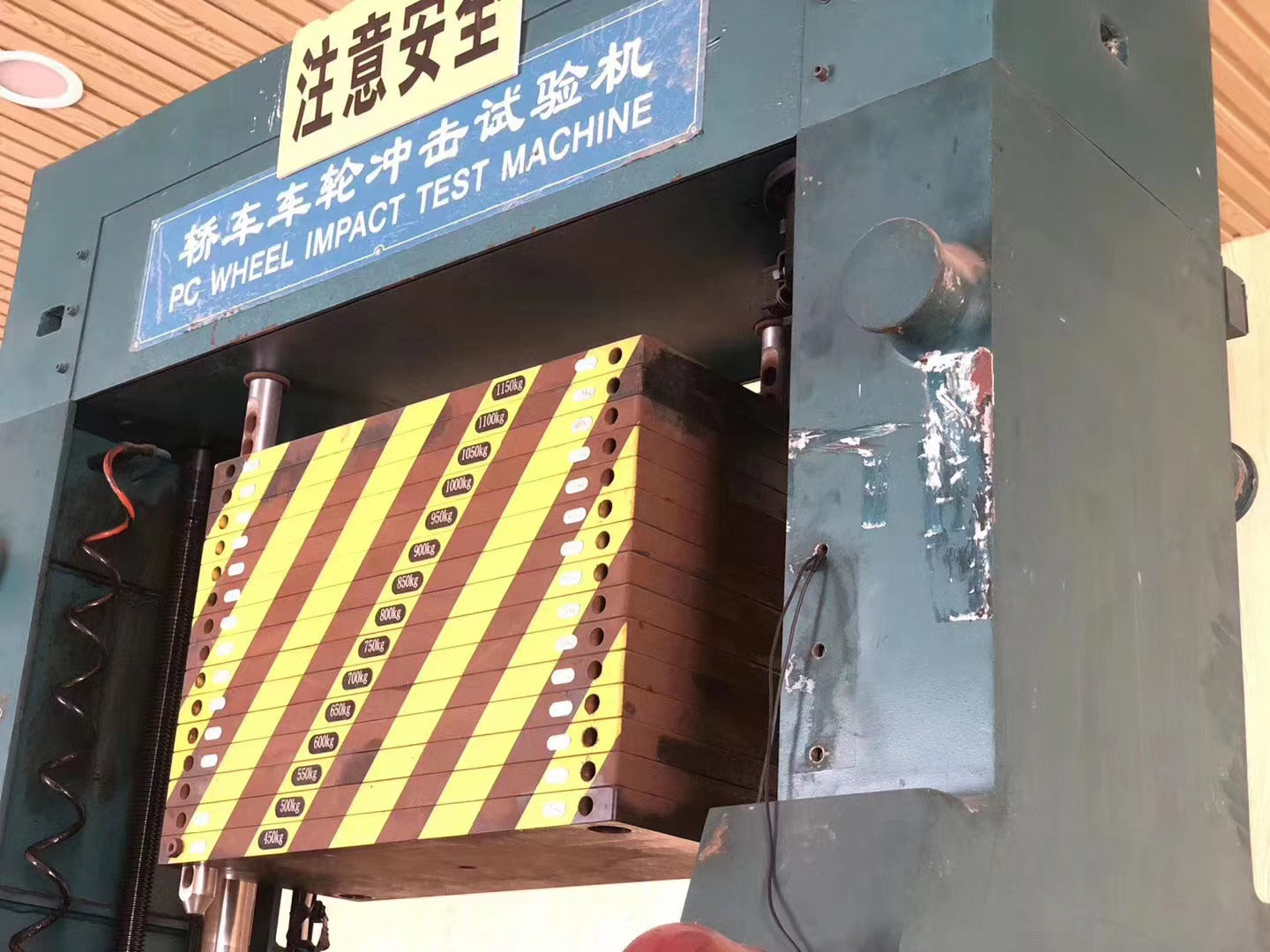
WE DO CARE
Safety Testing
Upon finalizing each design, we meticulously conduct strength, tensile, and fatigue tests on both the barrel and spokes, as well as the PCD, following TUV standards to ensure uncompromising quality and performance.